- September 11, 2017
- Posted by: SportsV
- Categories: Featured Articles, Features, Home News, Industry News, Interviews, News
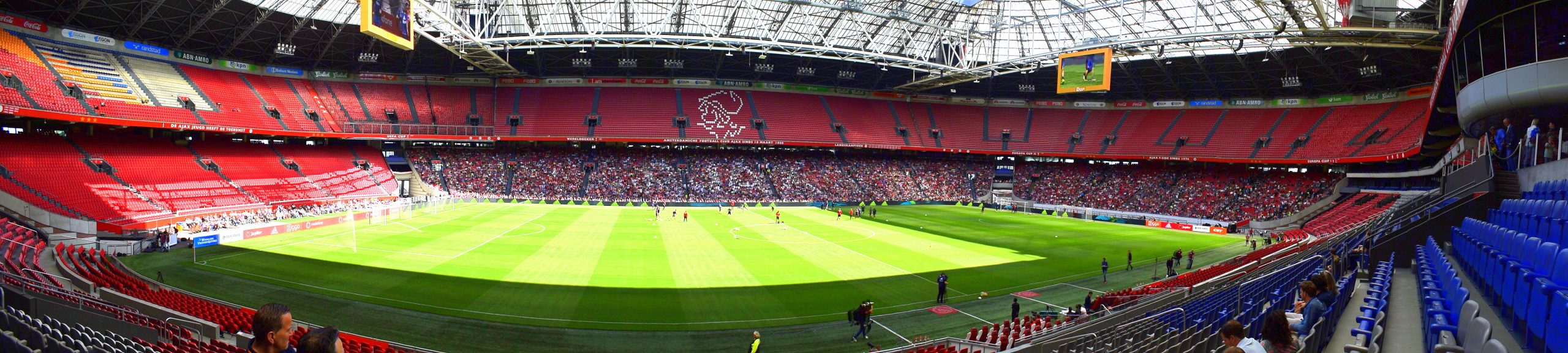
In the following Industry Interview, SVB’s Katie McIntyre hears insights from Henk van Raan, Chief Innovation Officer and Director Facility Management at the Amsterdam ArenA, as well as from Arjan Knottnerus, Co-owner and Managing Director of FieldTurf Benelux BV (a Tarkett Sports company).
Henk, the Amsterdam ArenA experienced yet another busy summer schedule this year, with the final concert, world-famous rock band U2 taking to the stage on the Sunday and the re-laying of the pitch commencing less than 24hrs later. Can you tell us more about the transformation and what it entailed?
We had a very tight schedule from the concert finishing at 11.30pm on Sunday night, when U2’s production company began the load out, so we had agreed with them that to complete the job quickly, they would put in place additional workers. This meant the load out was completed by 6pm the next day, whereas it would usually take 3 days, as it is a very big production. We started the re-turfing immediately after this, starting by preparing the under-layer with special machines.
The actual re-turfing began then at 9pm on the Monday, using the big rolls – 2.4m-wide by 10m-long – rolling them out one by one, and we were able to complete the job by 10am the next day. Obviously, it was not ready for play on at this stage, but the main task was done. From 10am Tuesday morning, the greenkeepers were able to start their job of mowing, putting the lines in, and adding the finishing touches, etc., with the pitch all complete by 4pm and ready for the 6pm training session. If it had been necessary, the pitch could even have been used for a match at that stage!
It was a very happy operation and it was very well prepared; every risk analysis was done before, we had everything double: double the man power, double machines, etc. We had the chillers for keeping the grass there, we did the harvesting the day before in the chillers to avoid traffic jams. It was a highly calculated operation and very high level management to ensure everything was on a critical path. No delays were possible, as we had just 2hrs spare; i.e. the pitch was completed at 4pm and the training session kicked off at 6pm!
This was quite a unique operation. We had done it once before, two years ago, but normally, ideally, we would like to have more time. Using double manpower, procedures, etc., means more potential risk and cost, but it shows both Ajax and the general public that we can deliver on such tight schedules. It was a calculated risk, but it meant a very profitable return, as in 2x U2 concerts, followed by the first training session at the stadium.
The Amsterdam ArenA opted for PlayMaster by Tarkett Sports, a carpet-based hybrid grass technology. What motivated you to choose this system?
This is the second time that we’ve used the hybrid version, having first used it last year. Our previous experience, knowing that the system delivers tremendous playability and durability, which is especially important for a venue like the Amsterdam ArenA, with our very high density programme. Sometimes, even during the football (soccer) season, we might have some concerts, and so far, we have learned that the hybrid system is the only one where you can combine, in several numbers, events on the same pitch during the football season.
For instance, this year we will have the Rolling Stones concert in September and after that, we have a dance event, AMF in October. Our goal is that we keep the pitch alive, so we will cover the pitch for these events, then we will do the required maintenance, and play on it afterwards. With a standard re-turfing, it’s very hard to do this and, in our experience, this is only possible with a hybrid pitch. You do need some precautions, but if you do it well, it’s doable.
This was a very strategic choice for us, because the hybrid is more expensive than the standard re-turfing, but for us it’s very valuable, because it means we can do concerts in between games; this is why it is the best option for us.
I take it you opted for the ready-to-play PlayMaster turf sods?
Yes, we did indeed opt for the ready-to-play PlayMaster turf sods system. Due to the short turnaround between the U2 concert and the first in-stadium training session from Ajax’s opponent Nice – with only 2 days in between – we needed the fastest possible turnaround, which meant choosing the ready-to-play solution.
Are there any other music events being hosted at the venue once the football season has started? How much time is needed for the pitch to recover after a concert?
Depending on the season (i.e. summer, autumn, etc.), and if you are at the start of the football season (i.e. when your pitch is in perfect condition), then it is possible to host 1-2 concerts, as long as we cover the pitch – as we have done before – then do the necessary maintenance to get rid of the divots, then after 1-2 days it’s back to full playability.
What is the intensity of use of the pitch at the Amsterdam ArenA?
If you look at our agenda, we have a very high intensity programme; every year we have 25 AFC Ajax games (our home tenant), 20 training sessions also from Ajax, then we have the Dutch National team, who play 4-5 games a year on the pitch, as well as 10 training sessions, plus up to 3 events on the pitch during the soccer season.
If you look at the whole agenda, we play football up until the first half of May, then we cover the pitch until around mid to late August, i.e. for 3 months, during which time we host up to 8-10 concerts and dance events at the Amsterdam ArenA. And then, when we do the replacement, we take the cover system away and we install the grass system to be ready for the next soccer season. So, you could say that 55 times a year, the venue is used for soccer, including matches and training sessions, and up to 10 concerts and dance events.
We have a very busy agenda, especially when you bear in mind that for concerts, you have building days, load-in and load-out, which means the stadium will be occupied for about 3-4 days per concert. So that means, for the 65 events a year on the pitch, including concerts, you can calculate it three times, which means the building and pitch is being used for more than 200 days. We are obviously kept extremely busy, but this is the reason why we are here!
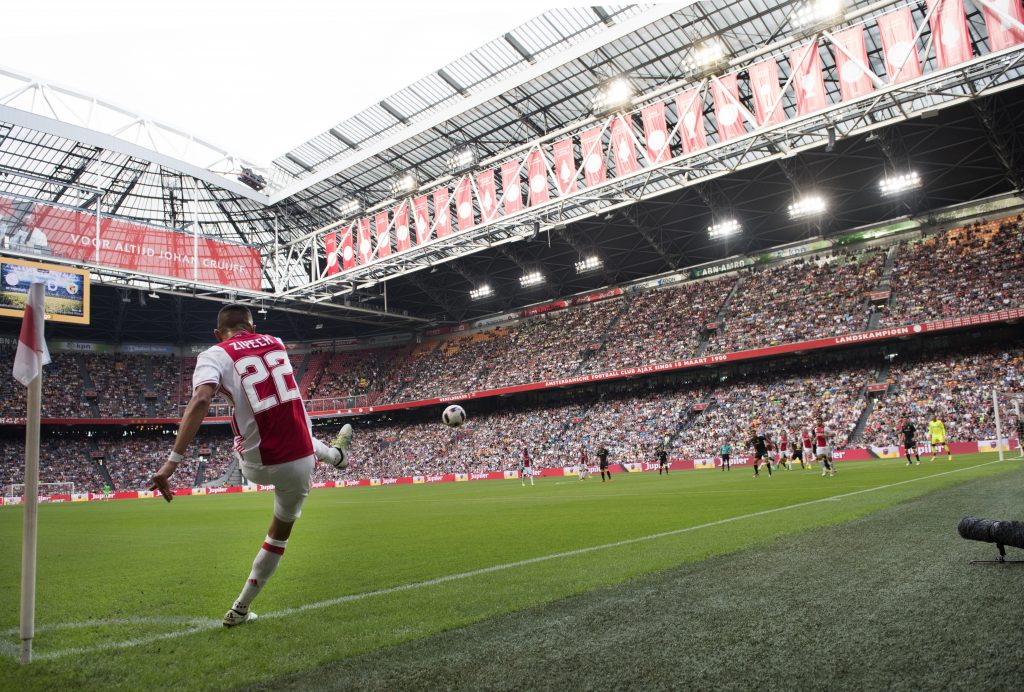
Does the PlayMaster pitch need any extra care? And are there any differences in terms of the cost of maintenance between a hybrid pitch and a natural grass pitch?
Although the PlayMaster pitch is around five times more expensive than a natural grass pitch initially, if you look at the day-to-day maintenance and the damage by using the pitch, it is less than with a standard pitch.
If you compare the two, and take the same programme that we run now but with a standard pitch, we would have to replace it twice or maybe even 3 times a year. Whereas now, with our PlayMaster hybrid, we only need one pitch a year. This saves us not only time, which means we can use these days for concerts, but it also gets rid of all the hassle of having to replace the pitch 2-3 times a year; taking it away and putting a new one in, etc. So the PlayMaster gives us a lot of rest and a much more controlled situation, rather than keep needing a re-turf.
In terms of recovering after damage to a hybrid pitch, there is actually less maintenance required because it is a sand-based system, an organic system, so we need to re-seed the pitch constantly during the season and use the artificial grow lights system, so we are able to have growth throughout the year, even in the winter. We can close the roof at night, so the temperature in the stadium can be maintained and allow pitch growth throughout the year, with regular grass seed sowing, use of fertilisers, etc.
At the Amsterdam ArenA, we have a digital pitch, with sensors measuring everything, from heating, humidity and grass plant growth activity to fertilisation, which all appears on the desktop. Instead of ‘green fingers’, the greenkeeper now needs a greater understanding of IT and how to utilise all of this available data and to make decisions in terms of the pitch maintenance and management programme. The job of the greenkeeper is certainly transforming; we now need them to be more tech savvy than green fingered!
In relation to the products we are employing, we are currently using the SGL grow lighting system, and we are also developing a new LED light concept, which is being tested in our Innovation Lab, and we expect that next year, we will have a full cover artificial lighting pitch system in our roof. This has never been done before, we are doing some testing and we have, mechanical wise, the system already, now we have to decide on the best type of LED to stimulate growth, using the covers, etc.
We are also doing some testing in a laboratory at HAS University of Applied Sciences in the south of the Netherlands, where we are using Philips LED lighting. We are doing some indoor testing and are now in a critical phase.
As for the pitch cover, we use a combination of aluminium panels for heavy-duty areas and Terraplas in all other areas.
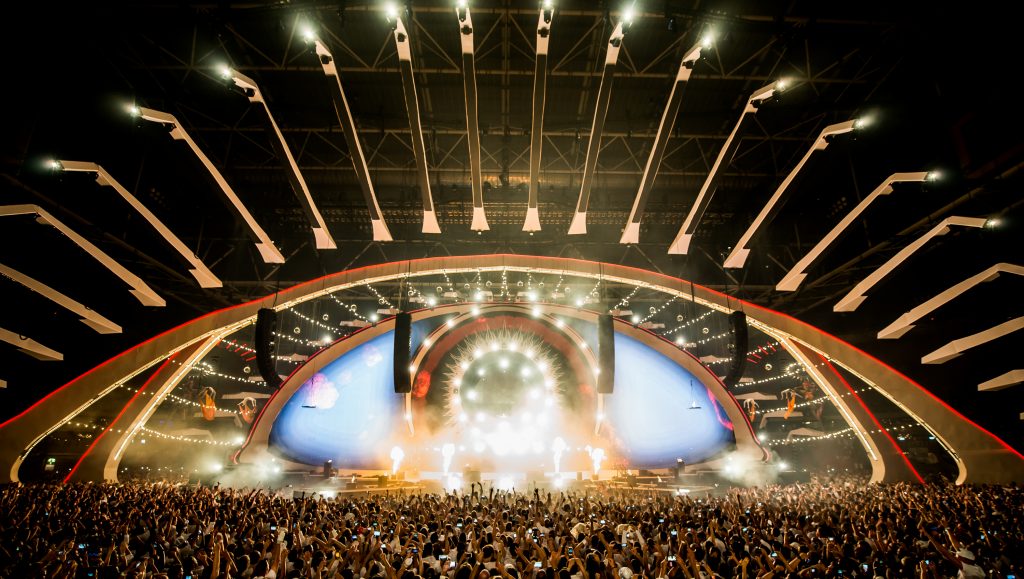
How do you judge the return on your investment for a football pitch? What are the main factors for a multipurpose stadium?
In general, you can say, if you are not using your building as a multipurpose venue, and only for one sport, say football for only 20 games, or whatever, then it does not make sense. It is a high cost building and if you only use it for 40 events, it’s not viable. However, when you are hosting the number of events that we are at the Amsterdam ArenA, then it is a more sustainable approach and a more sustainable business. We earn money every year and we re-invest this to ensure our building constantly remains state-of-the-art. Every feature that the customer expects, we want to deliver. Although our building is 20 years old, we always want to remain relevant and innovative, and make our building more sustainable. Usually all the money goes to the players and not on enhancing the spectators’ experience, we want all to be VIPs.
The stadium is currently undergoing a major transformation; we are investing a lot of money on escalators and widening our concourses; these investment costs are creating a better experience for spectators and enhancing accessibility. We are listening to our customers, not only in terms of what is needed today, but also tomorrow. We have an investment programme ready to deliver on this. It’s not always easy to find a ROI but this money is reserved already for investments for spectators. Every euro we earn, we put back into the building.
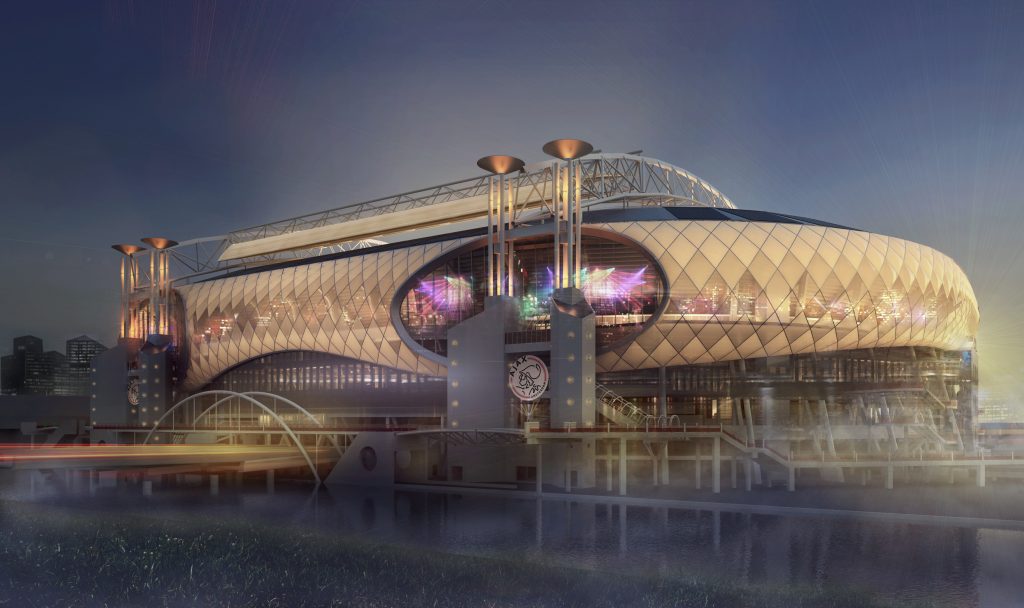
About Henk van Raan
Henk van Raan is Chief Innovation Officer and Director Facility Management of the Amsterdam ArenA and specialises in facility and project management. In his position, he is responsible for a variety of aspects such as real estate development, grass management, the Amsterdam Innovation Arena and sustainability.
On behalf of the Amsterdam ArenA, Henk has been responsible to define the ambition for the Amsterdam ArenA to become climate neutral by the year 2015. A goal the stadium has accomplished and has been warmly embraced by the City of Amsterdam, who have assigned the Amsterdam ArenA as a sustainability icon for the city.
Together with the municipality of Amsterdam, Henk is responsible for the Smart City development goals of the stadium and South East City District, which will have global impact in 2020. Henk is also a board member of Amsterdam Smart City.
The Amsterdam Innovation Arena is the most recent and very successful new development. Together with strategic partners: the City of Amsterdam, Microsoft, Huawei, Philips Lighting, KPMG, KPN, TNO, Nissan, BAM, Honeywell, Ballast Nedam, Eaton and HEINEKEN, the ArenA has developed and implemented new innovations for the stadium and its area.
The upcoming UEFA European Championships (EURO 2020), for which the Amsterdam ArenA will be one of the hosting stadiums, is a unique platform to showcase all these innovations. This tournament was also the catalyst that made the Amsterdam ArenA decide to make several revolutionary stadium adjustments and renovations towards 2020.
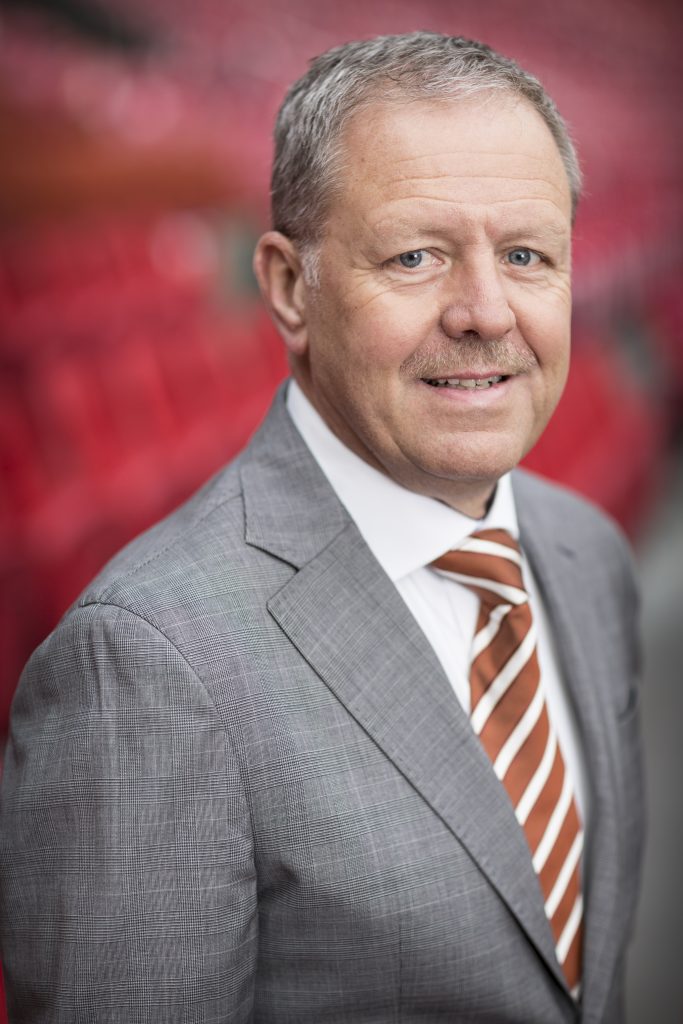
The other main driving force behind the delivery of this project was Arjan Knottnerus, Managing Director at FieldTurf Benelux BV, a Tarkett Sports company. SVB’s Katie McIntyre interviewed Arjan to find out more…
Arjan, can you please provide any additional information about this project – from the lead up to delivery, and going forward – as the installer?
Some five weeks ago, together with De Enk Groen & Golf and Hendriks Graszoden (the turf nursery), we completed the installation of the new hybrid grass pitch at the Amsterdam ArenA.
FieldTurf Benelux was the main contractor for this operation, which is Tarkett Sports’ contracting company for the Netherlands. We are a contracting company and have a contract with the Amsterdam ArenA for the re-turfing at the start of every season, as well as the contract to maintain the pitch with another contracting company, De Enk Groen & Golf, to keep it in the best condition throughout the season.
As a multifunctional stadium, the Amsterdam ArenA covers the pitch at the end of the soccer season for 2-3 months every summer on which to run their concert events, which means it is not possible for them to keep a natural grass pitch alive, so they start each new season with a new pitch. The ArenA wants to be able to use the ‘event floor’ for as long as possible, which sometimes means as little as 40hrs from the last concert to kick off for the first match on the new pitch.
The pitch is generally covered and transformed into an event floor from around the end of May until around early to middle of July, which means it would not be possible to keep a natural grass pitch alive. In the past, we used traditional sods – not the hybrid but the natural grass sods – but because of the growing conditions of the stadium and heavy use, the ArenA had problems keeping the pitch in high performance; even using the grow lights of SGL and the other solutions to keep pitches to the highest performance. As we were not able to deliver on the key objectives of stability and playability, the decision was made to go for a hybrid solution.
We had very little time after the concert and the stitched GrassMaster system – which is extremely durable – cannot be installed as a sod system, so the carpet-based PlayMaster system, which is available as lay-and-play sods was the obvious choice, especially as this allows for immediate play. As soon as this system became available, we began testing the PlayMaster hybrid sods and completed trials in some problem areas, like the goal mouths, and looked at how these performed compared to the traditional grass sods, and everyone was extremely satisfied with the results. So much so, that the Amsterdam ArenA decided to go for the hybrid lay-and-play PlayMaster system for the entire pitch for the 2016/17 season. We were in agreement and guaranteed the pitch would even be available for concerts during the soccer season, as long as the proper coverage, as in the Terraplas turf protection cover, was used. In 2016, they held their first concert in the stadium during the soccer season and the stadium was very satisfied with the pitch post-event; this was only possible due to the hybrid system.
This summer therefore marked the second time a full hybrid pitch had been installed at the stadium, which is home to AFC Ajax, their second team, and also the Dutch National Team. AFC Ajax’s first team train here once a week – which is not ideal, as obviously we’d all prefer they only played here for matches to keep the pitch in the best condition – and also play their home matches here, which would not be possible with the normal, traditional grass sods.
That means that last year, the ArenA hosted more than 90 games and training sessions, which meant little or no rest for the pitch, with around two training sessions or games a week! A big advantage of the hybrid solution is that it offers the players more stability and has a very good grip, which is important for the players to make them feel safe; with the normal grass sods, the Amsterdam ArenA had experienced problems with grip.
AFC Ajax has four GrassMaster hybrid pitches at their training facility, so, as they train on hybrid, they also wanted to be able to play their matches on hybrid. As it was not possible to have a GrassMaster in the stadium, we chose a hybrid PlayMaster system instead. Every week, we do measurements on all of the pitches, including stability, grip, shock absorption, etc., and compare and contrast the training and stadium pitches, as well as comments from the players, so we know if there are any specific changes the greenkeepers need to be make. We work in very close contact with AFC Ajax and the ArenA, hearing from the players and coaches as to what they say about the surfaces, then take this into consideration with what the measurements tell us, so that we can prepare the pitches in the best possible condition.
Important for the ArenA, if there is a re-turfing at the beginning of the season, if it’s laid down, we don’t have to wait 3 weeks before they can play on it, they can play directly on it; this is why it is called the PlayMaster lay-and-play system. You can literally lay it down and play on it directly, as Henk van Raan explained, the time schedules at the Amsterdam ArenA are extremely short. The quickest time we’ve done is 14hrs! It gives the ArenA a lot of flexibility, but the risks need to be managed. Being involved with a unique project like this, is something to be proud of.
Last year the stadium hosted one concert during the season and now this year they will host two; the Rolling Stones in September and then a big 2-day dance event in October. We have a special programme for concerts in terms of maintenance, with what we have to do before and after, this depends on the time of the year and the time channel we have after the concert. We actually have two different kinds of programmes depending on whether we have an AFC Ajax game two days after the concert or ten days after.
As you know, the Amsterdam ArenA has a digital pitch and we are now working on a dashboard that takes measurements 24/7, so we can know everything about the pitch, from weather to stability, we use the measurements to decide what to do in terms of pitch management and maintenance. The hope is eventually to have a dashboard that tells us what to do in the future and forecast what is going to happen, even telling us that a disease is coming up, or if we have a pitch that is an 8 and we want to bring it up to a 9.5, the dashboard can advise us what to do. This is a work in progress, it won’t happen today or tomorrow, but it is coming!
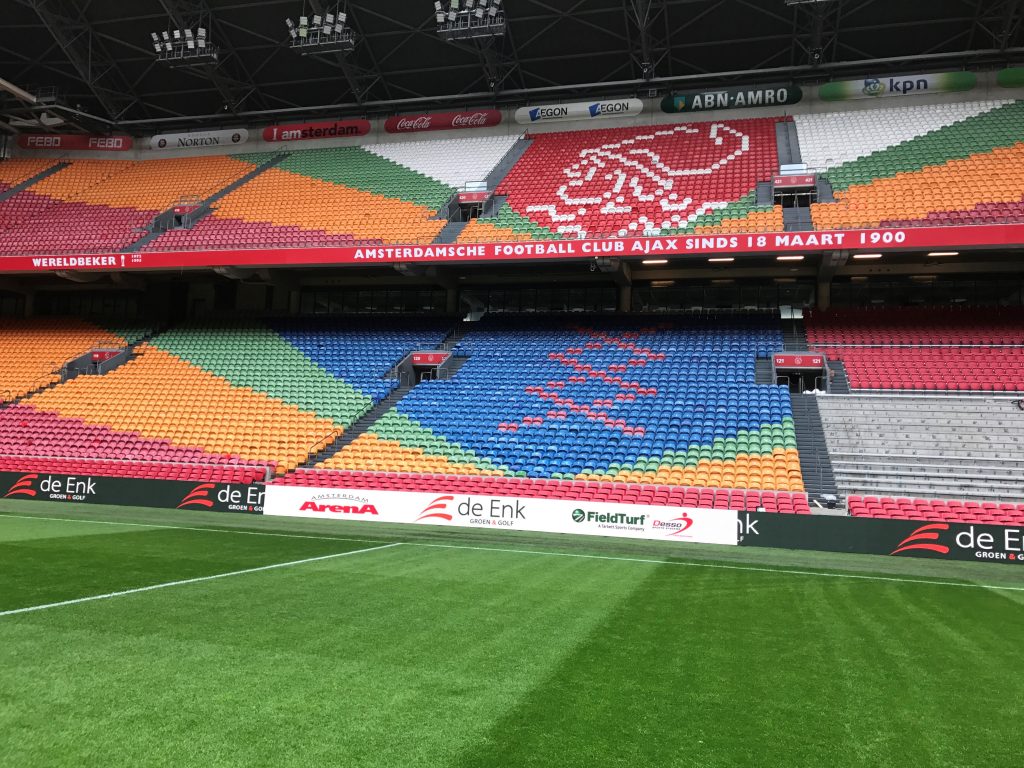
About Arjan Knottnerus
Arjan Knottnerus is Managing Director at FieldTurf Benelux BV, a Tarkett Sports company. Arjan is an entrepreneur through and through. He is co-founder of FieldTurf Benelux BV, a contracting and consulting company based in the Netherlands.
Arjan has years of experience in the construction and management of sports facilities with specialty natural and artificial grass. Besides entrepreneurship, Arjan is used to taking the initiative and can cooperate in a team environment as well, he is also decisive, customer-oriented, quality-oriented and creative. Because of his experience in the field of natural and artificial grass sports fields, Arjan also works as a consultant and shares his knowledge as a freelance lecturer.
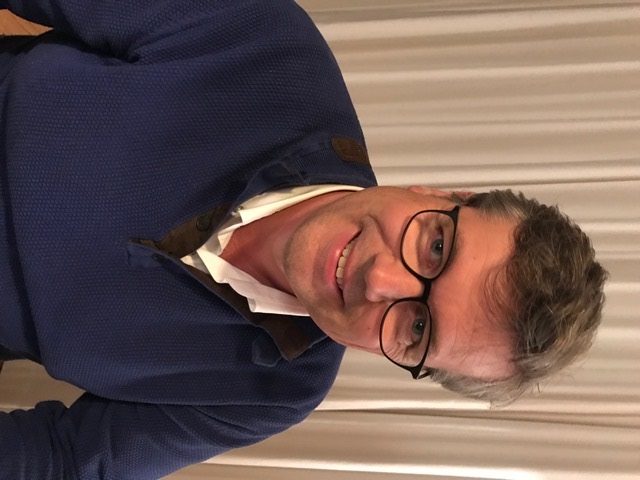

About GrassMaster
With GrassMaster and PlayMaster, Tarkett Sports continues to lead the sports grass industry offering both stitched and carpet-based hybrid grass technologies.
With PlayMaster, Tarkett Sports is dedicated to upholding the same high standards of quality performance for stadiums and training grounds today as it has been for years with GrassMaster.
Tarkett Sports is part of the Tarkett Group, a worldwide leader of innovative and sustainable flooring and sports surface solutions. Tarkett has one of the broadest global reaches of any flooring company in the world.
Find more information on GrassMaster and PlayMaster, the Hybrid Grass Solutions by Tarkett Sports, online at: www.grassmastersolutions.com