- June 10, 2024
- Posted by: John
- Categories: Case Studies, Featured Articles, Features, Home News, Industry News, News
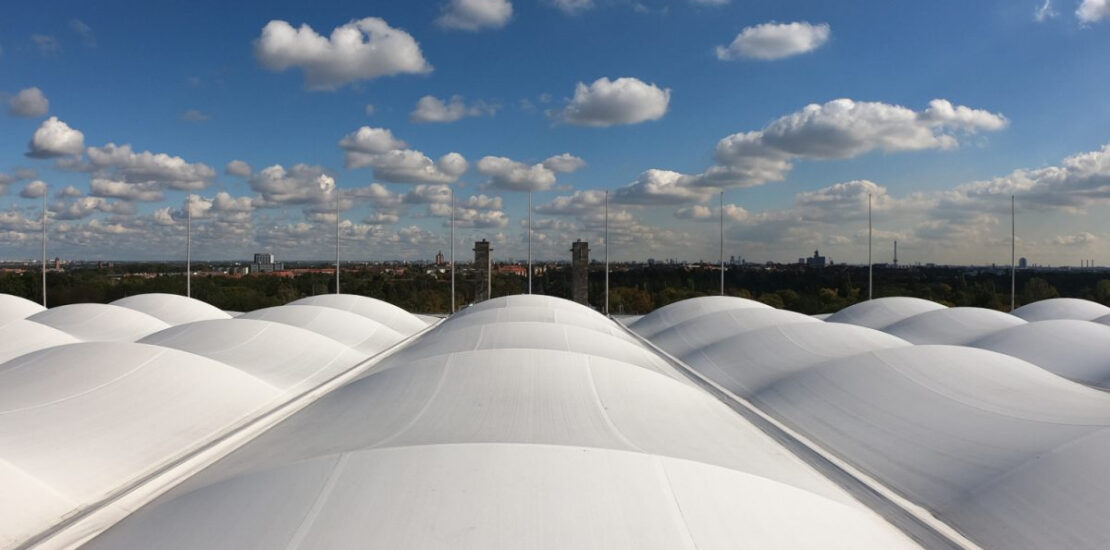
Football fans attending the final of the UEFA European Championships this summer can rest easy beneath the roof of Berlin’s Olympic Stadium come rain or shine, thanks to membrane experts Hightex Maintenance.
Stadium building has been transformed in recent decades with the move from glass or opaque materials to the use of membrane.
And membrane has helped to change the way the construction and architecture sectors think about building stadiums, allowing for more versatile and more environmentally friendly ways to construct or adapt major sporting venues.
Berlin Olympic Stadium is one example. In 2004, Bavarian membrane pioneers Hightex installed a membrane roof onto the brutalist venue built for the 1936 Olympics to give it a new lease of life and protect spectators from the weather.
The roof of the stadium is designed as a light cantilevering steel construction with an upper and lower membrane. The total length of the steel trusswork functioning as the main support is estimated at 68 metres and is visible through the translucent membrane.
With proper care and regular maintenance, the membrane structures, which can consist of ETFE (ethylene tetrafluoroethylene) or PTFE (polytetrafluoroethylene) are still in fantastic condition.
Hightex, which has recently changed focus to purely membrane maintenance after more than 30 years producing and installing membrane projects all over the world, is working its crew hard in the run up to the Euros, making sure the roof is in peak condition, patching any holes and tears in the material which have developed since their last inspection.
Liam O’Connor, Training Manager at Hightex Maintenance, stressed the importance of carrying out this regular care and maintenance to keep the materials in tip-top shape. He said:
I treat it like it’s a skin. If you look after your skin then the rest will be OK. Originally these structures were given a lifespan of 30 years, but we’ve been looking after a couple of roofs which are over 30 years old and still in fine condition.
All this started in the 1990s and a lot of these roofs are now supposed to be coming to the end of their lives, but if they’re properly looked after they could keep going for another 10 or 15 years. Nobody really knows because membrane as a working material has really only been around since the 1990s.
O’Connor explained how a typical maintenance programme, which is usually carried out twice a year, works.
We’re looking for holes, we’re looking for scratches, we’re looking for damage caused by other companies working up on the roof. We document everything, photograph it and repair it.
You get third parties up on the roof looking after their satellite dishes or their antennas or their cabling or motors and they tend to cause small amounts of damage and unfortunately they do make holes in it.
Human error isn’t the only problem O’Connor has to deal with, though. He added:
Then the crows come along and they pick at the material and make the holes bigger so a lot more water gets through. But we’ve got that under control because we come here twice a year now.
Maintenance first
Adam Mandrysz, COO of Hightex Maintenance, explained why the company had recently taken a strategic decision to move away from fabrication and installation into the maintenance market. He said:
It was a high-level management decision because they recognised more potential in maintenance than in the building market.
The main advantage we have is our long-term experience and knowledge of working with membrane materials. We can repair all kinds of damage and solve whatever problems come up.
We make a visual inspection of the stadium and we check all the welding details. We check the tightness and the weld integrity on the roof. Where we see it is starting to delaminate or isn’t properly sealed, those areas are marked and afterwards a maintenance team comes through to improve the quality of the sealings.
I would say the biggest enemy of membrane is constantly changing weather conditions – rain, snow, sunshine – and the temperature differences.
As well as its versatility and aesthetic appeal, membrane is, however, incredibly durable. Able to withstand the heat and desert life conditions of the Arabian Peninsula, it is also suitable for Central Asian winters, as proved by the Khan Shatyr Entertainment Centre in Kazakhstan, where temperatures can reach a low of -35 degrees Celsius.
A winning formula
The use of membrane provides a welcome solution to some of the construction industry’s toughest environmental challenges while at the same time offering unique visual character.
It may be a polymer-based material but it’s proven to be one of the most sustainable ways to cover structures such as sports stadiums and also airports, shopping centres, theatres, hotels, swimming pools, zoos and even areas on cruise ships.
According to some studies, the construction industry accounts for 50% of climate change. The use of concrete has a large part to play in this, itself accounting for up to 8% of global CO2 emissions.
But the construction industry’s impact is also down to embodied emissions of building materials, transportation of building materials, construction waste, soil and prefabricated components, and operation of equipment. The use of membrane can reduce the impact in every one of these areas.
Because membrane is lightweight as well as durable, the buildings enveloped with it do not need the same deep and heavy concrete foundations or steel structures to support it.
Membrane has a lower carbon impact when compared to polymer-based alternatives such as a polycarbonate canopy.
ETFE also offers free lighting. It transmits 95% of light giving 500lux daylight needed for indoor sports, avoiding the need for intensive daytime electric lighting. This is also enough light for plants to grow, so it is ideal for stadiums with grass pitches.
Tests also indicate that ETFE shows no signs of degradation from UV exposure.
There is also the very real possibility of reusing stadiums where membrane is the cladding/envelope of choice, whereby a structure can be dismantled from one location and reconstructed in a totally different part of the world. In certain cases, membrane can also be recycled at the end of its lifespan.
Al Bayt Stadium
Hightex has a wealth of experience in the fabrication and maintenance of membrane roofs and has been involved with projects including the retractable roofs on Wimbledon’s Centre Court and Poland’s National Stadium among others.
The company’s most significant recent project was the fabrication and installation of the iconic Al Bayt Stadium in Qatar for the 2022 FIFA World Cup.
Hightex was responsible for the membrane construction on the roof and façade of the venue which was built to resemble a traditional Bedouin tent.
The stadium can seat 68,000 spectators and it boasts a sustainable design with a unique retractable roof, ensuring optimal environmental efficiency.
Al Bayt is designed to look like, and is named after, bayt al sha’ar tents traditionally used by Qatar’s nomadic population. The inside of the stadium is fitted with a lighter inner membrane printed in part with a distinctive traditional Sadu geometric design on fabric with a Jacquard weave.
Mandrysz said:
It’s a unique stadium in terms of design and is an example of how membrane made a design come true. You couldn’t have made a stadium look like that with traditional building materials.
The advantages of using membrane are simple. The material is light and so the structure to support it relatively light as well. You don’t need a lot of support and you can cover big surfaces with a relatively light structure. Transportation costs are far lower. The installation is fast. The materials are translucent.
Minimal amounts of membrane can be used to cover a very large space when compared to glass or other materials. Hightex used 180,000m2 of installed membrane for the extraordinary Al Bayt ‘tent’ stadium. The cost of membrane is also a fraction of that of alternatives. Mandrysz added:
The energy needed to implement the structure is relatively low and emissions are lower. Transportation costs are also lower because you can fold all of the lightweight material. With proper maintenance you can use it for 40 or 50 years. At the end of its lifespan you can use the structure again and install a new cover.
Installation requires only a small specialist team, which can operate nimbly around other parts of the construction process – in contrast to the large teams of manual workers required when using alternative materials.
After installation of the structure had been completed, Hightex was tasked with carrying out a programme of maintenance on the venue. O’Connor added:
We try to carry out maintenance twice a year. Major maintenance takes place in January and February and the other maintenance around about September and October. It depends what’s going on and whether a tournament is taking place.
We like to keep the big maintenance for the winter because it’s just too hot otherwise. The climate in Qatar is a particular challenge.
O’Connor said the trend for membrane use in stadia isn’t going to go away. He added:
You’ve just got to look at Athletico Madrid’s Wanda Metropolitano stadium, which is PTFE in large parts, or Manchester City’s new training facilities which have PTFE on the outside.
Sports Venue Business has launched a raft of new offerings under the SVB LIVE banner for 2024, including Networking Events and a Webinar Series, the pinnacle of which being the 2024 SVB LIVE Conference & Exhibition. The next Networking Event is taking place at Marvel Stadium in Melbourne, Australia, on June 25th.
Check out the latest sports and entertainment venue development news in the exclusive, subscription-only, SVB Global Report here.
#SportsVenueBusiness – The leading platform for sector news, views & developments
#SVBLIVE – Elevating the Live Experience